Simulation
Der Digital Thread der Simulation in der Produktentwicklung
Management der Simulation während der gesamten Entwicklung
Für viele Jahre konzentrierte sich die Analyse nur auf einen bestimmten Schritt des Entwicklungsprozesses: die Verifizierung und Validierung. Heute hat sich die Simulation jedoch erweitert. Sie umfasst nun jede Phase des Entwicklungsprozesses, vom Konzeptdesign bis zu ausführbaren digitalen Zwillingen im Betrieb. Die Analyse liefert nun einen Mehrwert für die gesamte Produktentwicklung.
Die moderne Simulation umfasst jedoch unzählige Artefakte. Jedes dieser Artefakte besteht aus Modellen, Materialdefinitionen, Lasten, Randbedingungen und Ergebnissen, die sich mit unterschiedlicher Geschwindigkeit ändern. Die Analyseergebnisse sind das Ergebnis einer einzigen Version von jedem. Um gute Entscheidungen treffen zu können, müssen Ingenieure wissen, welche Konfiguration dieser Artefakte jedes Simulationsergebnis erzeugt hat. Andernfalls könnte eine Analyse der falschen Version eines Designs zugeordnet werden. Dies könnte zu einer falschen Entscheidung führen.
Der Simulation Digital Thread ist der Versuch, die Versionen der einzelnen Simulationsartefakte zu verfolgen und zu verwalten sowie zu wissen, welche Konfiguration zu welchem Ergebnis geführt hat. Wenn er ganzheitlich verwaltet wird, stellt er sicher, dass Ingenieure und Analysten richtig verstehen, welches Ergebnis für welches Design gilt. Der Simulation Digital Thread ist ein grundlegender Baustein für die Anwendung der Simulation in der gesamten Produktentwicklung.
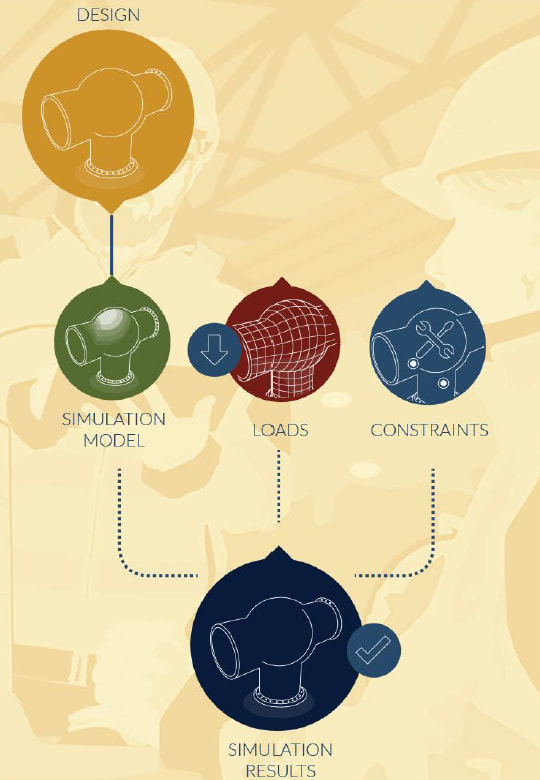
Systemsimulation im Systementwurf
Eine der ersten wichtigen Entwicklungsaktivitäten ist die Definition der Architekturen aller Systeme im Produkt. Systemingenieure entwerfen mehrere Optionen für jedes System. Dadurch können sie Alternativen im Designraum untersuchen.
Systemingenieure erstellen 1D-Simulationen, um die Machbarkeit der einzelnen Optionen zu testen und Handelsstudien durchzuführen. Analysten erstellen Systemsimulationsmodelle unter Verwendung von Bibliotheken mit gleichungsbasierten Komponenten. Systemingenieure verwenden diese Analysen, um neue Designs zu untersuchen und zu iterieren. So können sie bessere und fundiertere Entscheidungen über den Entwicklungsprozess treffen. Diese Analysen liefern Erkenntnisse, noch bevor detaillierte Designs existieren. Sie können schnell ausgeführt werden, sodass Ingenieure und Analysten schnell viele Architekturen untersuchen können.
Es ist schwierig, das Analyseergebnis jeder Iteration jeder Architektur für jedes Betriebsszenario im Auge zu behalten. Rückverfolgbarkeit ist entscheidend. Andernfalls weiß niemand, welche Ergebnisse welcher Architektur entsprechen, was den Entscheidungsprozess untergräbt. Außerdem ist dies nicht die einzige Anwendung dieser 1D-Systemsimulation. Sie entwickelt sich weiter und wächst mit den aufeinanderfolgenden Entwicklungsschritten. Dies ist ein früher Wertpunkt der Simulation Digital Thread. Die Nachverfolgung der Änderungen, die ein solches Wachstum kennzeichnen, ist entscheidend, da die an der Entwicklung Beteiligten verstehen müssen, welche Version des Modells für welchen Zweck verwendet wurde.
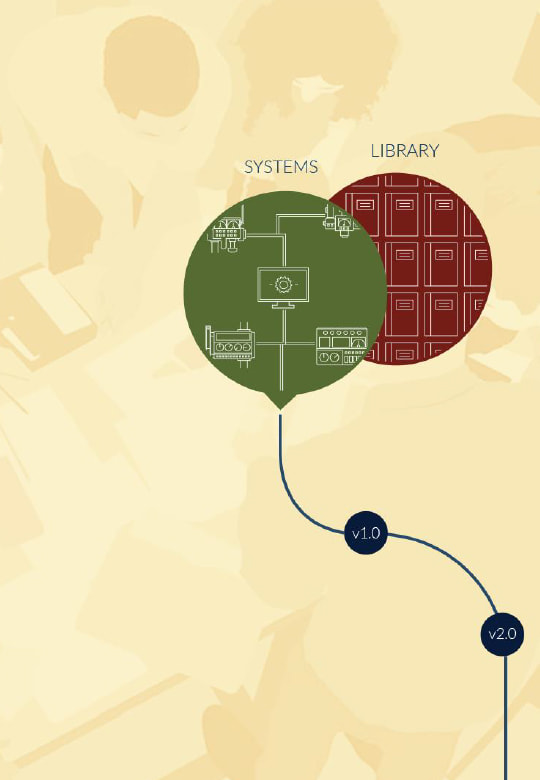
Konstruktionsentscheidungen mit
3D-Simulation
Sobald die Arbeit an der Detailkonstruktion beginnt, entwickeln die Ingenieure schnelle, genaue Analysen, um fundierte Entscheidungen zu treffen. Jede dieser Analysen konzentriert sich auf verschiedene Arten der technischen Physik, einschließlich Flüssigkeiten, Wärmeübertragung, Strukturen und vieles mehr. Jede dieser Analysen wird von 3D-Modellen abgeleitet, die sich im Laufe der Konstruktion verändern und weiterentwickeln. Die Assoziativität, die es ermöglicht, Änderungen am 3D-Modell in das Analysemodell zu übertragen, spart viel Zeit.
Die Konfiguration jeder Simulation, auch wenn sie einfach sein mag, wird schnell kompliziert. Jedes Analysemodell kann von einer anderen Version der Konstruktion abgeleitet sein. Jedes verwendet andere Lastfälle und Randbedingungen. Die Assoziativität ermöglicht die schnelle Weitergabe von Änderungen. Dies bietet ein leistungsfähiges Mittel, um Analysen gegen Designänderungen schnell durchzuführen. Ohne diesen Kontext wenden Ingenieure jedoch Schlussfolgerungen aus einem Satz von Analyseergebnissen auf ein anderes Design an. Das wiederum führt zu einer falschen Designentscheidung.
Dies ist ein weiterer Punkt, der den Wert des Simulation Digital Threads ausmacht. Ingenieure und Analysten verwalten 3D-Modelle, Simulationsmodelle, Lasten und Randbedingungen als Teil einer einzigen, ganzheitlichen, nachvollziehbaren Analysehistorie. So ist sichergestellt, dass jeder weiß, welche Analyseergebnisse für welche Design-Iteration gelten.
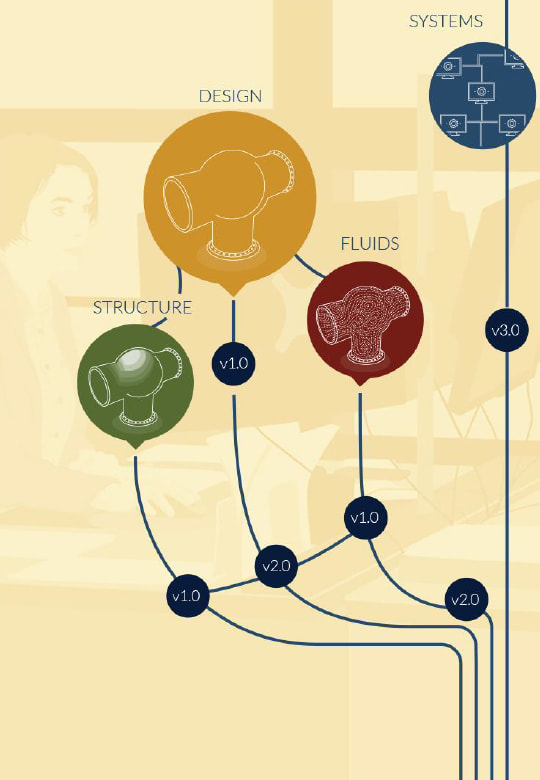
Detaillierte Trade-Offs und Design-Exploration
Zu Beginn der Entwicklung entwickeln die Systemingenieure Produktarchitekturen mit den dazugehörigen Anforderungen. Mechanische, elektrische, elektronische und Software-Ingenieure verwenden diese Architekturen und Anforderungen als Input für ihre detaillierte Arbeit. Während des Designs untersuchen die Ingenieurteams Optionen, um diese Einschränkungen anzupassen oder neue Alternativen zu entdecken. Bei dieser Tätigkeit sind verschiedene Arten von Simulationen nützlich.
Eindimensionale (1D) Systemsimulationen werden zu Beginn der Entwicklung verwendet, um Leistungsabwägungen zwischen den Architekturen vorzunehmen. Detaillierte Multiphysik-Simulationen kommen ebenfalls ins Spiel, um das Verhalten vieler physikalischer Domänen genau zu erfassen. Beide ermöglichen eine automatisierte Design-Exploration und Trade-Off-Studien, bei denen Designkontrollen und Leistungsparameter variieren. Dies bietet eine potente neue Möglichkeit, Anforderungen und Beschränkungen für Ingenieurteams mitten in der Entwicklung anzupassen.
Diese Analysen haben viele bewegliche Teile. Sie beinhalten Analysemodelle, Komponentendefinitionen, Lasten, Randbedingungen, Ergebnisse und mehr. Durch die Verwaltung dieser Artefakte als Teil des Simulation Digital Threads wissen Ingenieure und Analysten genau, welches Ergebnis welchem Design entspricht. Das wiederum ermöglicht es ihnen, wertvolle und aufschlussreiche Entscheidungen zu treffen.
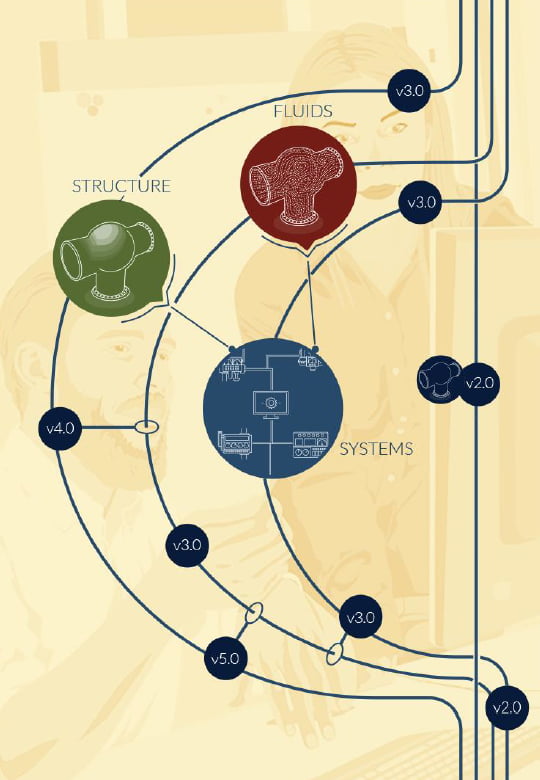
Simulation zur endgültigen Verifizierung
vor dem Test
Die Verwendung von Analysen zur Verifizierung und Validierung ist eine der ältesten Anwendungen. Dennoch ist sie immer noch eine der wertvollsten. Die Idee besteht darin, High-Fidelity-Simulationen durchzuführen, um sicherzustellen, dass die Entwürfe die Anforderungen erfüllen, die Einschränkungen einhalten und wie vorgesehen funktionieren. Das Ziel ist es, nur einen einzigen Prototyp für physische Tests zu bauen und zu testen.
Wie beim Analysemodus in der Detailkonstruktion werden die High-Fidelity-Simulationsmodelle in dieser Phase direkt aus 3D-Modellen erstellt. Dennoch gibt es signifikante Unterschiede. Diese Analyseläufe umfassen zahlreiche Lastsätze und mehrere Stapel von Randbedingungen. Solche Modelle müssen gleichzeitig den Einfluss mehrerer physikalischer Domänen berücksichtigen. Die Genauigkeit ist von größter Bedeutung und erfordert präzise Materialmodelle und andere Phänomene wie Kontakt.
Die komplexen Modelle, die für die Verifizierung und Validierung erstellt werden, haben viele Komponenten, die sich unabhängig voneinander ändern. Um sicherzustellen, dass die Prototypen die physikalischen Tests im ersten Durchgang bestehen, ist es wichtig zu wissen, welche Analyseergebnisse mit welcher Designversion übereinstimmen. Die Verwaltung all dieser Komplexität als Teil des Simulation Digital Threads liefert die richtigen Informationen zur richtigen Zeit für die richtige Entscheidung.
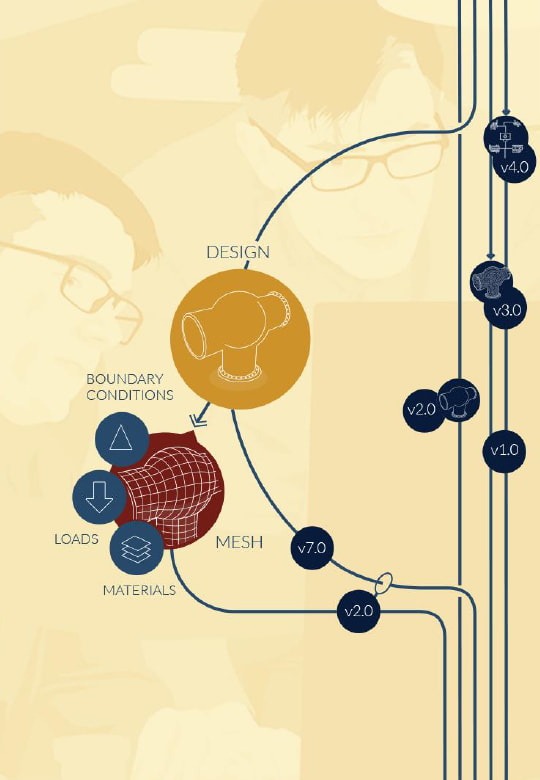
Prototyping verbundener Produkte mit Analyse
In den letzten Jahren haben immer mehr Unternehmen damit begonnen, intelligente Produkte mit Internet-of-Things (IoT)-Plattformen zu verbinden. Dadurch können sie Daten austauschen und innovative neue Strategien wie Fernüberwachung und Produkte-as-a-Service umsetzen.
Das Design und die Entwicklung intelligenter, vernetzter Produkte stellt neue Herausforderungen an die Verifizierung und Validierung. Die Prüfungen müssen die Leistung des Produkts und die Konnektivität mit einer IoT-Plattform umfassen. Auf physische Tests zu warten, um die Integration zu verifizieren, ist eine risikoreiche Angelegenheit. Misserfolge führen zu kostspieligen Iterationen durch physische Prototypen.
Digitales Prototyping ist ein jahrzehntealtes Konzept zur virtuellen Überprüfung der Designleistung vor den physischen Tests. Bei der Anwendung auf IoT-Konnektivität speist die physische Hardware des Produkts die Sensormesswerte in die 1D-Systemsimulation ein. Diese wiederum ahmt das Verhalten des Produkts nach. Die Simulation sendet dann visuelle Sensordaten an die IoT-Plattform. Auf diese Weise können Unternehmen die Verbindung eines Produkts mit der IoT-Plattform virtuell prototypisieren.
Diese Simulationen haben viele Teile, die verwaltet werden müssen. Die Konfiguration der physikalischen Hardware, der 1D-Simulation und der IoT-Plattform spielen alle eine Rolle. Die Verfolgung und Verwaltung dieser Teile als Teil des Simulation Digital Threads schafft Vertrauen in die Entscheidungen, die auf dem digitalen Prototyping basieren.
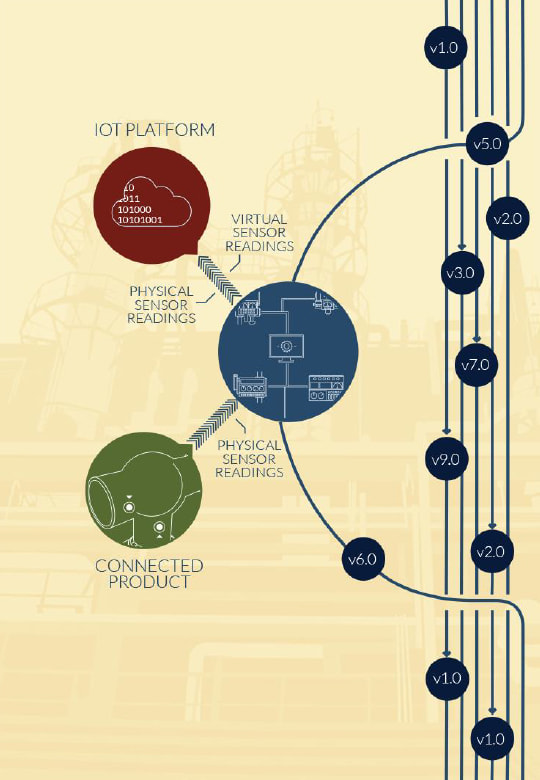
Hybride digital-physikalische Simulationen zum Testen
Die meisten Diskussionen über den Einsatz von Simulationen während der Entwicklung konzentrieren sich auf das digitale Prototyping. Das bedeutet, dass ausschließlich mit digitalen Analysen gearbeitet wird, bevor ein physischer Prototyp zum Testen verwendet wird. Einige Unternehmen erforschen Möglichkeiten, digitales Prototyping und physische Tests zu mischen und zu kombinieren, um beides zu verbessern.
Diese Anwendung der Simulation kann zahlreiche Formen annehmen. Ein physisches elektronisches Steuergerät (ECU) kann mit einer 1D-Systemsimulation verbunden werden, um das richtige Verhalten zu verifizieren. Sensormesswerte aus einem physikalischen Test können in eine detaillierte Transientenanalyse einfließen, um die Genauigkeit zu maximieren. In diesen und anderen Fällen verschmelzen Unternehmen eine idealisierte digitale Simulation mit dem physikalischen Verhalten des Produkts. So können sie mit der Validierung beginnen, lange bevor sie einen physischen Prototyp haben.
Diese hybriden digital-physikalischen Setups haben viele Teile, von denen jedes eine Version hat, die sich im Laufe der Zeit ändert. Es ist wichtig, das Ergebnis dieser Tests im Zusammenhang mit dem physischen Prototyp und den digitalen Simulationsversionen zu verfolgen. Ohne sie ist die Ursache für den Restfehler unklar. Ohne Klarheit sind Korrekturmaßnahmen nicht möglich. All diese Punkte müssen als Teil des digitalen Simulations-Threads verwaltet werden.
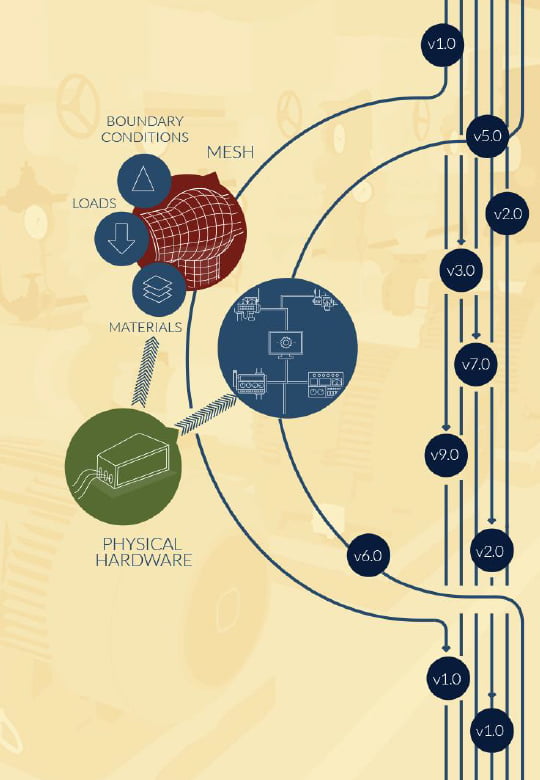
Betrieb eines digitalen Zwillings eines Betriebsprodukts
Durch die Verbindung von intelligenten Produkten mit IoT-Plattformen erhalten Unternehmen Einblicke in den Betrieb von Produkten im Feld. Diese neue Fähigkeit ist eine wichtige Voraussetzung für die "Products-as-a-Service"-Modelle, die ganze Branchen revolutionieren.
Während physikalische Sensordaten Einblicke bieten, schränken physikalische Einschränkungen, extreme Temperaturen oder andere Zwänge die Möglichkeit ein, Sensoren an optimalen Stellen zu platzieren. Hier nutzen die Ingenieure die Simulation auf innovative Weise. Sie speisen Sensormesswerte in eine 1D-Systemsimulation ein, nehmen virtuelle Sensormesswerte aus der Analyse und speisen sie in die IoT-Plattform ein. Die Kombination aus physischen und virtuellen Sensoren kann neben IoT-Plattformen in der Cloud als ausführbare Digital Twins auf dem Produkt laufen.
Solche Szenarien stellen einen komplexen Fall für das Konfigurationsmanagement dar. Das komplette, in Betrieb befindliche Produkt im Feld hat eine spezifische Konfiguration. Die 1D-Systemsimulation muss entsprechend angepasst werden, da sie genau dieses Produkt nachbilden muss. Die Simulation kann sogar Modelle reduzierter Ordnung für komplexere Analysen enthalten. Wenn diese nicht genau nachverfolgt und als Teil des digitalen Simulations-Threads verwaltet werden, sind die Erkenntnisse der IoT-Plattform nicht genau.
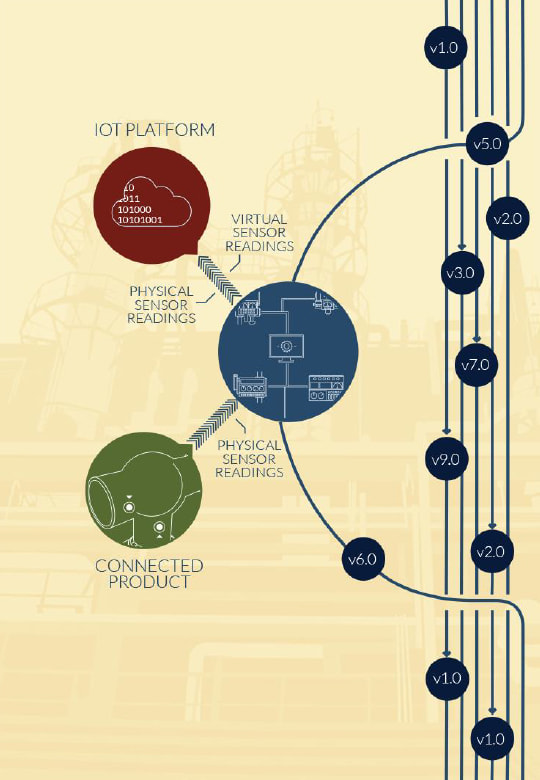
Erfahren Sie, wie Simcenter Ihre Kreativität freisetzt und Ihnen die Freiheit gibt, innovativ zu sein.
Das könnte Sie auch interessieren
Sie haben Fragen?
Wir beantworten sie gerne. Zögern Sie nicht, sich mit uns in Verbindung zu setzen.
Kontakt aufnehmen